The need to respond to an unanticipated process aeration requirement in a fast, cost effective manner is a dilemma that occasionally confronts every wastewater treatment plant operator.
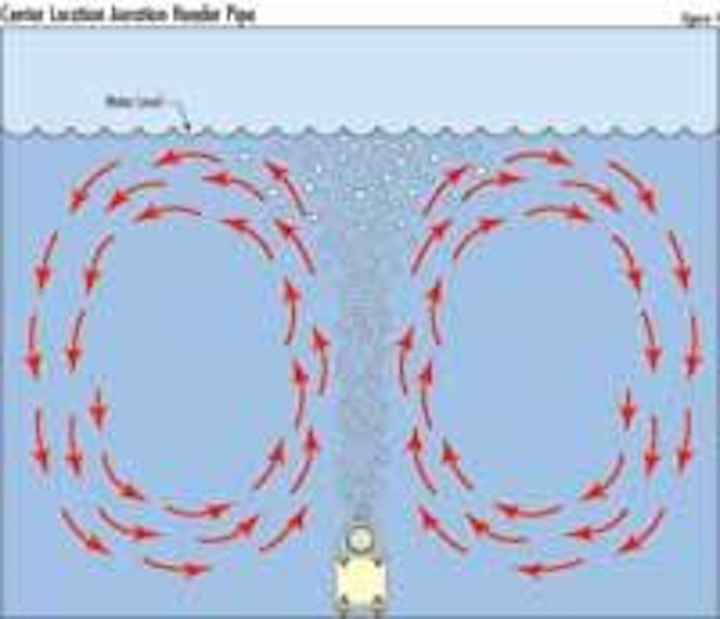
By Steve Deiters
The need to respond to an unanticipated process aeration requirement in a fast, cost effective manner is a dilemma that occasionally confronts every wastewater treatment plant operator. This is especially true at facilities operating with limited and fixed budgets.
![]() |
A typical need is to retrofit an existing unused tank to fulfill newly developed requirements or to adapt a temporary tank. Examples include adapting a tank to provide equalization or digester duties to help out at peak demand times.
Although there are a wide variety of diffusers available that can provide application specific aeration capabilities, coarse bubble diffusers with a check valve design can be the best choice when the goal is an aeration system that is simple to design and easy to fabricate and install in a vertical format.
Coarse bubble diffusers with their rubber diaphragm cap and check valve feature have been used for decades with great success in pre-engineered package wastewater treatment plants and municipal facilities. They are perhaps the most adaptable style of air diffusers available.
The success of coarse bubble diffusers can be traced to the simplicity of their design and the many features they offer. The diffusers provide good mass transfer for biological processes and also are good mixing devices. Since the diffusers are plastic with molded EPDM rubber check valve diaphragms they are inexpensive and readily available.
The simplicity of the diffuser check valve design minimizes the back flow of wastewater (and debris carried with it) into the piping, which can cause potential long term operational problems. Also, since they are vertical format diffusers, they lend themselves well to installations using inexpensive Sch. 80 PVC pipe for aeration headers. A properly sized threaded connection, either 3/8" NPT or 3/4" NPT thread depending on the model and size of the diffuser, located at the 12 o’clock position is all that is needed to properly position the diffuser for installation.
System Sizing
![]() |
When sizing these systems to determine the volume of air required it is best to use the Ten States Standards of aeration for mixing and equalization tanks as a foundation. The standard requires 25 to 35 CFM per 1000 cubic feet of volume. In most cases not only does the volume of air meet the mixing needs of the application as stated by the standard, but it also may meet or actually exceed the dissolved oxygen requirement of the biological system. Since the needs vary depending on the application, it is better to be more conservative when sizing the air flow requirement.
The number of diffusers required for a given installation is determined by two factors. The first is the total air volume being delivered. A good rule of thumb is to take half of the total operational range of the diffusers (typically 3 to 12 CFM) and divide it into the total CFM required. This will give you the number of diffusers required and provide the flexibility to deliver more air in the future if the challenges of the application change.
The second factor is the spacing of the diffusers. This parameter is driven by the number of diffusers coupled with the liner feet of aeration piping needed to form the grid. Good design practice dictates that the spacing can range from about a foot to not more than 2 1/2 feet. The closer the diffusers are together the better, as long as the spacing is evenly distributed. Diffusers can be closer than the general guideline minimum if the flow rate and overall sizing of the system demands.
If the spacing is excessive, based on the total CFM and optimal diffuser flow range ratio, then more diffusers can be added with no problem during the design phase to narrow the spacing gap. Having diffusers located in as many places as possible can be just as important as having a sufficient flow of air for the volume of the tank and can actually enhance the overall performance of the system. Since diffusers are relatively inexpensive, the quantity can be increased with no appreciable impact on the overall cost of the system while enhancing the performance as well as increasing the flexibility of the system.
The sizing of the aeration piping is also important when finalizing the system design. Its diameter is determined by the total air flow of the system measured in cubic feet per minute. Since most coarse bubble systems are used in smaller tanks and the air flow rate is low, a 2" Sch. 80 pipe is typically suitable for most applications. Smaller diameter pipe (3/4" or 1") technically could be used but it is not advisable. It is important that the pipe has a large enough diameter to allow diffuser installation without obstructing the air flow, and has sufficient material thickness to allow the 3/8" NPT or 3/4" NPT pipe threads to be tapped into the pipe.
Larger air flows may require larger diameter pipes or a combination of sizes to accommodate the increased flow rate. The design considerations are simple, but overall good engineering practice must be followed for an effective installation on a larger scale. For those applications with larger volumes of air it is best to contact the diffuser manufacturer for guidance.
Layout, Installation
The layout of the aeration piping is driven by the shape of the tank and the overall flow rate. The placement of the pipes is determined by 1:1 to 2.2:1 ratio of the width of the tank to the depth of the water. In other words if the tank has water depth of 9’ then the maximum distance from the pipe to the tank wall or the next aeration pipe should not exceed 19.8 feet. It is always advisable to design on the conservative side. The closer the aeration piping headers are together and the more that are used, the better the overall performance of the process with enhanced mixing and rolling action. These guidelines are true whether the tank is round or rectangular.
The piping system must be secured to the tank floor using pipe stands that locate the aeration pipes slightly above the bottom - usually about 6-8". The pipe stands act as a restraining device and keep the diffusers high enough off the floor so that solids in the process don’t settle out and cover the diffusers. Pipe stands also provide a method for leveling the piping system, since the floors of tanks are typically not level.
Leveling of aeration piping is important for a successful installation. If there is more than one header in the tank running off the same manifold it is important that they are level, and multiple aeration headers must define the same plane. This will insure even distribution of the air flow and the development of a good aeration pattern that promotes mixing and biological activity.
The sch.80 PVC aeration pipe is easily cut and fitted in the field if needed although some diffuser manufacturers offer complete piping systems and related hardware such as pipe stands in a pre-engineered kit form for simplified end-user installation.
Air Sources
In retrofit or secondary applications there may be a surplus of blower capacity available on hand that can be diverted to the tank. Care must be taken, however, to make sure that the water head in the second tank is equal to any other outlets for the designated blower. Often operators prefer to dedicate the operation of an isolated smaller blower system to make for a completely independent operating system because of the flexibility such a system offers. Often times the supplier of the aeration systems can be a source for the blower package and control systems if needed. In that way there is single source responsibility for the entire system.
![]() |
Summary
The retrofitting of smaller aeration tanks need not be a long drawn out experience nor does it need to be expensive. It offers the operator a chance to use existing unused facilities with a minimum of capital expenditure and fulfill a need for the successful operation of the entire plant. With these systems a “win/win” situation is created on many levels.
About the Author:
Steve Deiters is president of Diffused Gas Technologies Inc. of Lebanon, OH, a manufacturer of fine and coarse bubble air/gas diffusers and systems used in the water and wastewater treatment industries. He has held marketing, project management, and technical positions with pollution control equipment manufacturers such as Pollution Control Inc. and Clow Waste Treatment Division as well as capital equipment manufacturers serving the process and electronics industries. Deiters is a Bachelor of Science graduate of the University of Cincinnati.
Post a Comment
Post a Comment